
OLED Production Systems for R&D

- Developing organic EL materials
- Developing high-polymer materials
- Developing phosphorescent materials
- Developing organic thin-film solar cells
- Developing organic electronics devices, etc.

Appearance
|
 |
Overall views
|
* Our company can design and provide the system according to the customers' specifications. For details, click here to contact us.

Line-up of film coating systems for developing organic materials (PDF : Japanese)
http://www.kitano-seiki.co.jp/product/organic/KVD.pdf

- The same room can be used to form films from organic or metal materials.
- Deposition by co-evaporation of organic and metal materials is enabled.
- Deposition by co-evaporation of organic materials is enabled (Max.: 4 elements).
- The system is equipped with a water-cooling jacket for preventing a mixture of organic and metal materials.
- In the deposition room, substrates and masks can be replaced in a vacuum environment.
- The gap between the substrate and the mask is minimized.
- The substrate rotation mechanism achieves an in-plane film thickness distribution of ±5%.
- The organic deposition cell excels in directional characteristics and reduces material contamination in the deposition room.
- A special surface coating is applied over the inner surface of each processing room, which shortens the time to achieve the target vacuum environment pressure.
- The system can be connected to a glove box system.
- PLC control enables automated transfer and exhaustion.
- In the standard state, the load lock room can accommodate a total of five substrates and mask holders.
- A substrate heating room is incorporated for pre-processing.

System configuration |
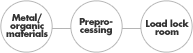 |
No. of film Deposition rooms |
1: Used for both organic and metal materials |
Deposition sources |
8 for organic and 2 for metal materials. |
Substrate size (inch) |
2 |
Film thickness resolution
(Å/s) |
0.0057 Å/s (with CYGNUS made by INFICON) |
No. of film thickness sensors |
4: Used for both organic and metal materials |
Cooling system for
film thickness sensors |
Water-cooling (The chiller controls temperature at an accuracy of 0.01°C.) |
Deposition by co-evaporation
of organic materials |
Enabled (A unique control method allows a dope mixture ratio of 0.1 to 30wt% when host materials are deposited at 1Å/s.) |
In-plane distribution (%) |
In a 50mm diameter area, ±3% for organic films, and ±5% for metal films |
Preprocessing room |
1 (for heating substrates) |
No. of racks
in the load lock room |
5 |
Ultimate
pressure (Pa) |
Deposition
room |
10-6 class |
Load lock
room |
10 |
Vacuum
evacuation
system |
Deposition
room |
Cryo pump |
Preprocessing
room |
Cryo pump |
Load lock
room |
Dry pump |
|
Dry pump (roughing vacuum pump) |
Input power source |
3φ 200V 130A |
Automated exhaustion |
Enabled (optionally)
|
Automated vent |
Automated transfer |
Automated vapor deposition |
Substrate heating
during vapor deposition |
Enabled (optionally) |
Glove box connection |
Enabled (optionally) |
Space required
for installing
only the system |
3800×1200 |



- Developing organic EL materials
- Developing high-polymer materials
- Developing phosphorescent materials
- Developing organic thin-film solar cells
- Developing organic electronics devices, etc.

Appearance
|
 |
Overall views
|
* Our company can design and provide the system according to the customers' specifications. For details, click here to contact us.

Line-up of film coating systems for developing organic materials (PDF : Japanese)
http://www.kitano-seiki.co.jp/product/organic/KVD.pdf

- The system is equipped with a water-cooling jacket for preventing a mixture of organic and metal materials.
- In the deposition room, substrates and masks can be replaced in a vacuum environment.
- The gap between the substrate and the mask is minimized.
- The substrate rotation mechanism achieves an in-plane film thickness distribution of ±5%.
- The organic deposition cell excels in directional characteristics and reduces material contamination in the room.
- A special surface coating is applied over the inner surface of each processing room, which shortens the time to achieve the target vacuum environment pressure.
- The system can be connected to a glove box system.
- In the standard state, the load lock room can accommodate a total of twelve substrates and mask holders.
- PLC control enables automated transfer and exhaustion.

System configuration |
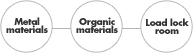 |
No. of deposition rooms |
1 for organic materials, and 1 that is used for both organic and metal materials |
Deposition sources |
8 + 6 for organic materials and 3 elements for metal materials |
Substrate size (inch) |
2 |
Film thickness resolution
(Å/s) |
0.0057 Å/s (with CYGNUS made by INFICON) |
No. of film thickness sensors |
4 sensors for each room |
Cooling system for
film thickness sensors |
Water-cooling (The chiller controls temperature at an accuracy of 0.01°C.) |
Deposition by co-evaporation
of organic materials |
Enabled (A unique control method allows a dope mixture ratio of 0.1 to 30wt% when host materials are evaporated at 1Å/s.) |
In-plane distribution (%) |
In a 50mm diameter area, ±3% for organic films, and ±5% for metal films |
Preprocessing room |
- |
No. of racks
in the load lock room |
4X3 (rows) |
Ultimate
pressure (Pa) |
Deposition
room |
10-6 class |
Load lock
room |
10-5 class |
Vacuum
evacuation
system |
Deposition
room |
Cryo pump |
Preprocessing
room |
- |
Load lock
room |
Turbo molecular pump |
|
Dry pump (roughing vacuum pump) |
Input power source |
3φ 200V 150A |
Automated exhaustion |
Enabled (optionally)
|
Automated vent |
Automated transfer |
Automated vapor deposition |
Substrate heating
during vapor deposition |
Enabled (optionally) |
Connection with
a glove box system |
Enabled (optionally) |
Space required
for installing
only the system |
3900X1200 |



- Developing organic EL materials
- Developing high-polymer materials
- Developing phosphorescent materials
- Developing organic thin-film solar cells
- Developing organic electronics devices, etc.

Appearance
|
 |
Overall views
|
Estimate |
KVD-OLED Evo.Cluster |
|
* Our company can design and provide the system according to the customers' specifications. For details, click here to contact us.

Line-up of film coating systems for developing organic materials (PDF : Japanese)
http://www.kitano-seiki.co.jp/product/organic/KVD.pdf

- The 3-axis robot mechanism enables the transfer of masks and specimens.
- The transfer room can optionally be equipped with a substrate holder vacuum sealing mechanism.
- Deposition by co-evaporation of organic materials is enabled (Max.: 4 elements).
- Vapor deposition of eight types of organic materials can be prepared in the same room.
- Two organic deposition rooms are incorporated. This allows 16 organic deposition sources to be installed.
- The system is equipped with a water-cooling jacket for preventing a mixture of organic and metal materials.
- In the deposition room, substrates and masks can be replaced in a vacuum environment.
- The gap between the substrate and the mask is minimized.
- The substrate rotation mechanism achieves an in-plane film thickness distribution of ±5%.
- The organic deposition cell excels in directional characteristics and reduces material contamination in the deposition room.
- A special surface coating is applied over the inner surface of each processing room, which shortens the time to achieve the target vacuum environment pressure.
- The system can be connected to a glove box system.
- Plasma substrate cleaning is enabled in the preprocessing room.
- In the standard state, the load lock room can accommodate a total of six substrates and mask holders.
- PLC control enables automated transfer, exhaustion, and vapor deposition.

System configuration |
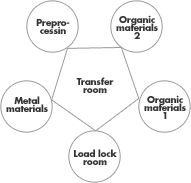 |
No. of film deposition rooms |
2 for organic and 1 for metal materials |
Deposition sources |
8 X 2 for organic and 5 for metal materials |
Substrate size (inch) |
2 |
Film thickness resolution
(Å/s) |
0.0057Å/s (with CYGNUS made by INFICON) |
No. of film thickness sensors |
8 for organic and 2 for metal materials |
Cooling system
for film thickness sensors |
Water-cooling (The chiller controls temperature at an accuracy of 0.01°C.) |
Deposition by co-evaporation
of organic materials |
Enabled (A unique control method allows a dope mixture ratio of 0.1 to 30wt% when host materials are Deposited at 1Å/s.) |
In-plane distribution (%) |
In a 50mm diameter area, ±3% for organic films, and ±5% for metal films |
Preprocessing room |
1 (Plasma cleaning) |
No. of racks in the load lock room |
12 |
Ultimate
pressure (Pa) |
Deposition
room |
10-6 class |
Load lock
room |
10-5 class |
Vacuum
evacuation
system |
Deposition
room |
Cryo pump |
Preprocessing
room |
Turbo molecular pump |
Load lock
room |
Turbo molecular pump |
|
Dry pump (roughing vacuum pump) |
Input power source |
3φ 200V 200A |
Automated exhaustion |
Standard feature |
Automated vent |
Standard feature |
Automated transfer |
Standard feature |
Automated vapor deposition |
Standard feature |
Substrate heating
during vapor deposition |
Enabled (optionally) |
Connection with
a glove box system |
Enabled (optionally) |
Space required
for installing
only the system |
2000X2000 |



- Developing organic EL materials
- Developing high-polymer materials
- Developing phosphorescent materials
- Developing organic thin-film solar cells
- Developing organic electronics devices, etc.

Appearance
|
 |
Overall views
|
* Our company can design and provide the system according to the customers' specifications. For details, click here to contact us.

Line-up of film coating systems for developing organic materials (PDF : Japanese)
http://www.kitano-seiki.co.jp/product/organic/KVD.pdf

- The transfer mechanism allows the transfer of masks and specimens.
- The same room can be used to form films from organic or metal materials.
- Deposition by co-evaporation of organic and metal materials is enabled.
- Deposition by co-evaporation of organic materials is enabled (Max.: 4 elements).
- The system is equipped with a water-cooling jacket for preventing a mixture of organic and metal materials.
- In the deposition room, substrates and masks can be replaced in a vacuum environment.
- The gap between the substrate and the mask is minimized.
- The substrate rotation mechanism achieves an in-plane film thickness distribution of ±5%.
- The organic deposition cell excels in directional characteristics and reduces material contamination in the deposition room.
- A special surface coating is applied over the inner surface of each processing room, which shortens the time to achieve the target vacuum environment pressure.
- The system can be connected to a glove box system.
- PLC control enables automated transfer and exhaustion.
- In the standard state, the load lock room can accommodate a total of five substrates and mask holders.

System configuration |
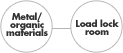 |
No. of deposition rooms |
1: Used for both organic and metal materials |
Depositon sources |
6 for organic materials and 3 for metal materials |
Substrate size (inch) |
2 |
Film thickness resolution
(Å/s) |
0.0057Å/s (with CYGNUS made by INFICON) |
No. of incorporated film
thickness sensors |
4: Used for both organic and metal materials |
Cooling system for
film thickness sensors |
Water-cooling (The chiller controls temperature at an accuracy of 0.01°C.) |
Deposition by co-evaporation
of organic materials |
Enabled (A unique control method allows a dope mixture ratio of 0.1 to 30wt% when host materials are evaporated at 1Å s.) |
In-plane distribution (%) |
In a 50mm diameter area, ±3% for organic films, and ±5% for metal films |
Preprocessing room |
- |
No. of racks
in the load lock room |
5 |
Ultimate
pressure (Pa) |
Deposition
room |
10-6 class |
Load lock
room |
10 |
Vacuum
evacuation
system |
Deposition
room |
Cryo pump |
Preprocessing
room |
- |
Load lock
room |
Dry pump |
|
Dry pump (roughing vacuum pump) |
Input power source |
3φ 200V 75A |
Automated exhaustion |
Enabled (optionally)
|
Automated vent |
Automated transfer |
Automated vapor deposition |
Substrate heating during
vapor deposition |
Enabled (optionally) |
Connection with
a glove box system |
Enabled (optionally) |
Space required
for installing
only the system |
2600X1200 |


|